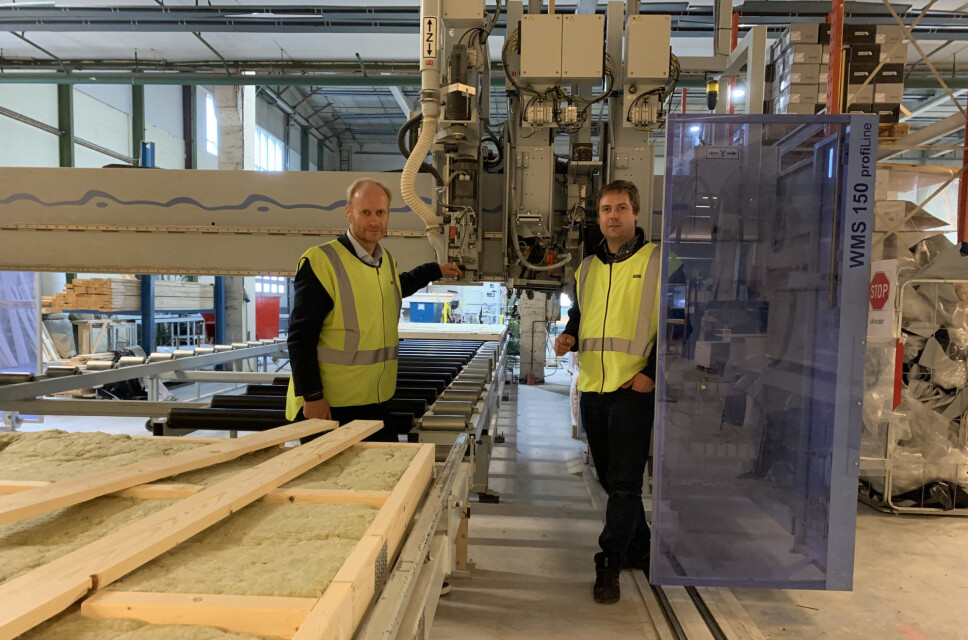
Automatiserte og doblet omsetningen
Støren Treindustri har gått fra å omsette for 150 til 300 millioner kroner siden 2011. Hovedsuksessfaktoren er at bedriften har investert stort i automatisert produksjon. I tillegg bygger de stadig høyere hus. Det lønner seg.
Artikkelen er skrevet av WoodWorks! Cluster.
– Alle som driver med precut har en Hundegger-sag. Vi har tre, starter administrerende direktør Rune Johnsen og viser fram en av de mest avanserte vidundrene. De siste ti årene har han brukt over 40 millioner kroner på automatiserte maskinlinjer som produserer byggesett i tre både raskere og mer presist.
Nesten 3D-printing
Stadig mindre sages og bankes på byggeplassen. Å sette opp bygg handler i dag mer om å montere elementer som kommer mest mulig ferdige på lastebil. Støren har vært dyktige og hengt med på trendene. Og elementproduksjonen deres har altså blitt svært effektiv og rasjonell med store avanserte maskiner som «tryller» byggeoppskriften om til ferdige elementer med dyktige maskinoperatører ved spakene bak blant annet Hundeggeren.
– En Hundegger er det nærmeste du kommer en 3D-printer for bygg i tre. Den undersøker oppskriften i datafila for produktet, tar det som fins i «plankehaugen» og lager det. Det er en svært optimal produksjon, forteller teknisk sjef Per Gunnar Nordløkken. Det er han som har ansvar for alt det dyre utstyret. Han viser automatiserte linjer både for yttervegger, innervegger og bærevegger, og selvsagt gulv- og takelementer. – Og med tre Hundeggere har Støren god kapasitet på denne typen elementproduksjon eller rene såkalte precut-leveranser, påpeker han.
Vil opp i åtte etasjer
En annen suksessfaktor er at bedriften har våget seg fra bakkeplan og opp i høyden. Fra 1990-tallets eneboliger for Block Watne har bedriften fulgt med markedstrenden og levert stadig større og mer kompliserte bygg, som rekkehus og lav blokkbebyggelse på tre og fire etasjer. Det har gitt større oppdrag og dermed økt omsetning.
Dette gir mersmak, og nå vil de opp på nye høyder. Et nytt prosjekt til 17 millioner kroner skal utvikle gode løsninger for å produsere hus på opptil åtte etasjer hos Støren.
– Økt urbanisering og fortetning krever enda høyere bygg. Til nå har slike høyhus i tre vært ensbetydende med massivtre eller limtre. Det er mange fordeler med massivtre i forhold til stål- og betongbygg, men det tradisjonelle bindingsverket tilfredsstiller også de fleste av disse. I tillegg er det enda lettere enn massivtre. Det er et pluss både når elementene skal transporteres og monteres, men særlig hvis bygget settes opp på bæresvak grunn som fins mange steder her i landet, understreker direktør Johnsen.
Samarbeider om nye standarder
Til prosjektet har Johnsen og co fått nærmere syv millioner kroner i støtte fra Forskningsrådet og Skogtiltaksfondet over tre år. Støren skal samarbeide med både forskere og bygg-entreprenører som blant annet Johnsen og Nordløkken finner sammen med i nettverket sitt gjennom treklyngen WoodWorks! Og nye løsninger skal prøves ut underveis.
– Det er få såkalte preaksepterte løsninger for bygg i bindingsverk i den høyden – altså få standarder og mange utfordringer. Særlig er kravene til lyd og brann sammen med konstruksjonssikkerhet krevende. Ofte fordi de virker mot hverandre. Og gjør de ikke det, er gjerne løsningen for dyr, forklarer teknisk sjef Nordløkken. Målet er at prosjektet skal jobbe fram tekniske løsninger som både er konkurransedyktige og mulig å produsere.
Skal teste løsningene
Støren samarbeider med SINTEF som startet allerede i sommer med å kartlegge kjente løsninger som idéene om nye konstruksjoner kan hvile på. – Etter hvert vil dette testes ut i lab og vi vil også simulere og teste før vi prøver ut gode idéer enkeltvis i prosjekter. Til slutt vil vi sette opp en pilot som kan teste ut hele konseptet, – fra hvordan det er å produsere, transportere og montere modulene, til hvordan de tekniske løsningene virker i det ferdige bygget, oppsummerer Nordløkken.
– Og selvsagt om kunden blir fornøyd. Kundekravene er ikke tekniske, men vi vil alltid passe på at produktet er tilpasset sluttbrukeren og markedet, skynder Johnsen seg å legge til. Han har opplevd siste årene at det ofte handler mest om fleksibilitet. Rett og slett å ha en ramme som gjør at kunden kan ombestemme seg og forandre prosjektet underveis, hvis markedet endrer seg. – Kanskje starter byggherre opp et prospekt med familieleiligheter med mange rom, mens det i løpet av en seks måneders byggeprosess viser seg at markedet heller vil ha mindre parleiligheter. Med fleksible løsninger kan vi da tilpasse byggprosjektet utviklingen i markedet, illustrerer selgeren i Johnsen.
Nye gode karbonlagre
Det nye prosjektet vil ikke bare gi Støren nye forretninger, men har som mål å sikre hele bransjen de byggtekniske løsningene som skal til for å produsere høyere bindingsverksbygg i klimavennlig tre – i konkurranse med mindre miljøvennlige materialer. – I Trøndelag binder skogen mer karbon enn vi forbruker og trebygg er effektive karbonlagre. Klima og miljø verdsettes hos kundene, men bare hvis byggene er like gode og rimelige. Og det skal vi få til. Vi er riktignok ikke der at vi har karbontall på elementene våre ennå, men vi tilfredsstiller kundenes krav til BREAM (europeisk standard for miljøvennlighet i bygg). Tre er jo miljøvennlig i seg selv, understreker Johnsen.
Gulroten for Støren med å være med å dra dette prosjektet er imidlertid forspranget. – Innovasjonsarbeidet er åpent med en del statlig støtte og skal selvsagt komme hele treindustrien til gode. Vår belønning for å være med å dra lasset er at vi vil bli de første ut på hoppkanten med åtte etasjers treblokker i bindingsverk her til lands, avslutter Støren-direktøren.